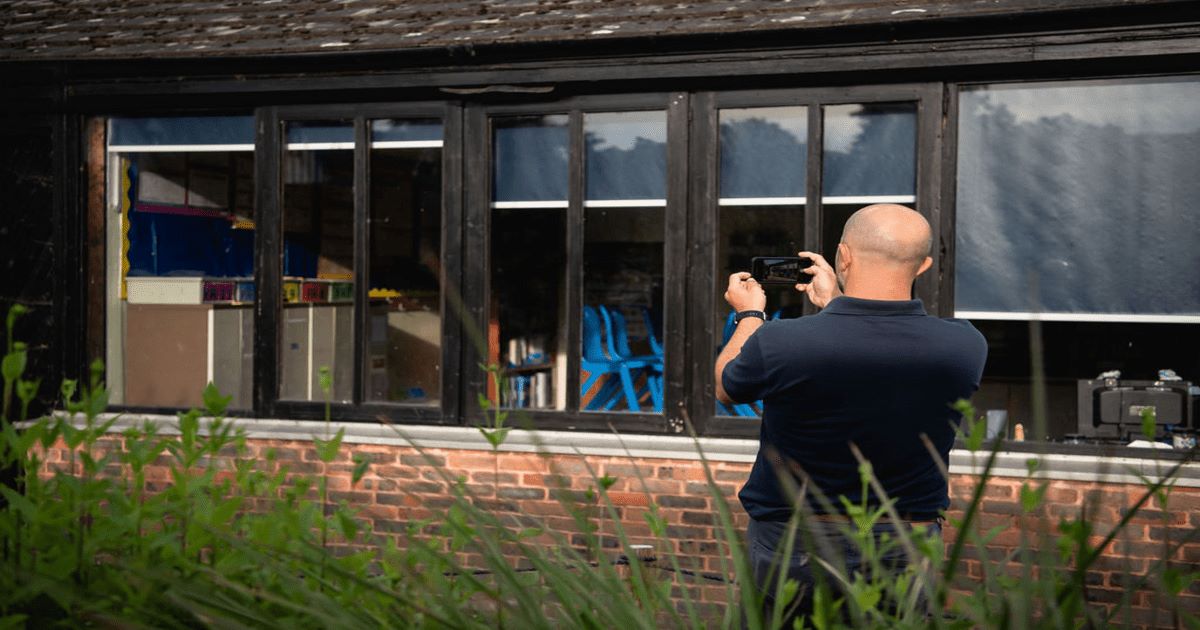
What is RAAC?
RAAC is a lightweight concrete used in various buildings that is made from a combination of cement, lime, water, and an aeration agent. The mixture is poured into moulds and then subjected to high pressure and heat, known as autoclaving, to create a lightweight, strong, and porous material.
Although it is concrete it is very different from traditional concrete because of the way in which it was made.
The useful life of such (panels) has been estimated to be around 30 years. As such, there are concerns about the safety and structural integrity of RAAC buildings especially in schools.
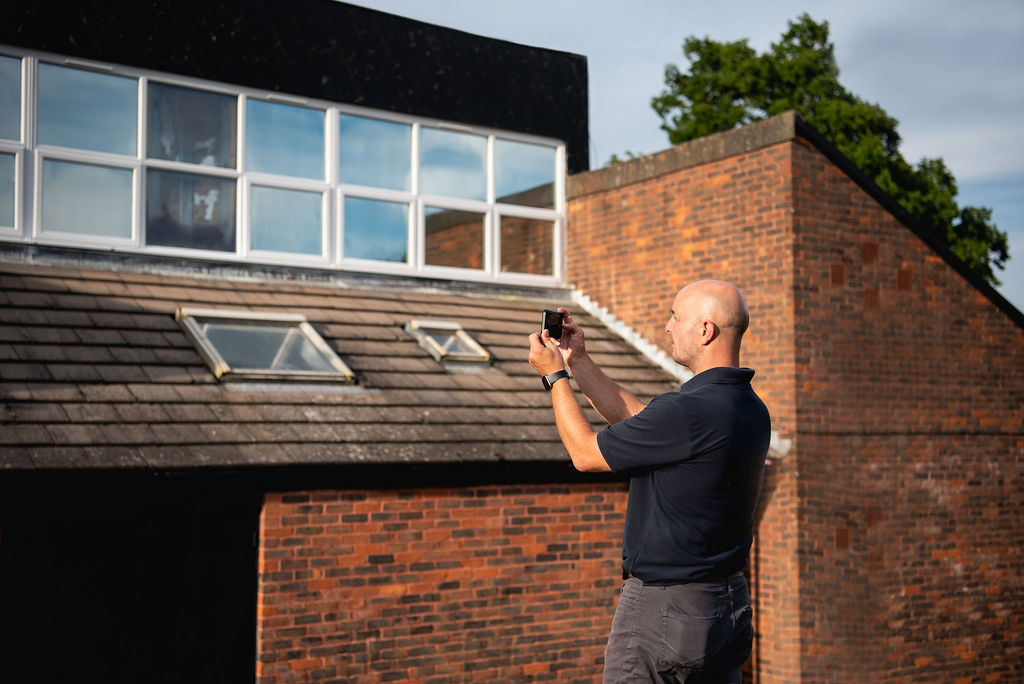
Where is RAAC found?
Schools, hospitals and various other public buildings constructed within the 1950s to the mid-1990s. Numerous contractors were using RAAC across the UK.
The National Audit Office (NAO) report earlier this year said the concrete had been confirmed in at least 65 schools in England. With reports from NHS providers identifying 14 of its hospitals, which wereconstructed "either wholly or in major part with RAAC". Seven of these are considered "critical" and not fit for purpose beyond 2030.
When was RAAC identified?
Use of RAAC in schools was confirmed in 2018 when the roof of a primary school in Kent collapsed. 24 hours after identification of structural weakness. Four schools in Essex and the north-east of England were shut in April and June after RAAC was discovered in their ceilings. Surveys to determine the presence and condition of the RAAC used in the buildings have been taking place since March last year. In June, ministers launched a UK government-wide inquiry into the use of RAAC in public buildings to look into how many of the thousands of government buildings were constructed with it.
Why is RAAC Dangerous?
Material and construction deficiencies identified with RAAC have raised concerns regarding performance in structural applications when compared to traditional concrete. This increases the risk of structural failure, which can be gradual or sudden with no warning. Sudden failure of RAAC panels in roofs, eaves, floors, walls and cladding systems would be dangerous, and the consequences could be serious. The material is also more prone to collapse when wet, which can happen if there are leaks in a building’s roof.
What are the features of RAAC?
- Panels have low compressive strength, being around 10-20% of traditional concrete, meaning strength is reduced. This strength is further impacted by water saturation.
- It is very porous and highly permeable. This means that the steel reinforcement within the panels is less well protected against corrosion ‘rusting’ than steel reinforcement in traditional concrete.
- The reinforcement within RAAC panels is less well bonded to the surrounding concrete. The dominant connection is via secondary reinforcement.
- No ‘coarse’ aggregate, therefore it is less dense than traditional concrete; being around a third of the weight.
- RAAC has reduced ’stiffness’ characteristics resulting in high displacements, deflections, and sagging.
- The bearing of planks is often insufficient, by comparison to modern standards, which presents a significant risk.
- There was limited quality control during manufacture and installation meaning there is a high degree of variability between panels.
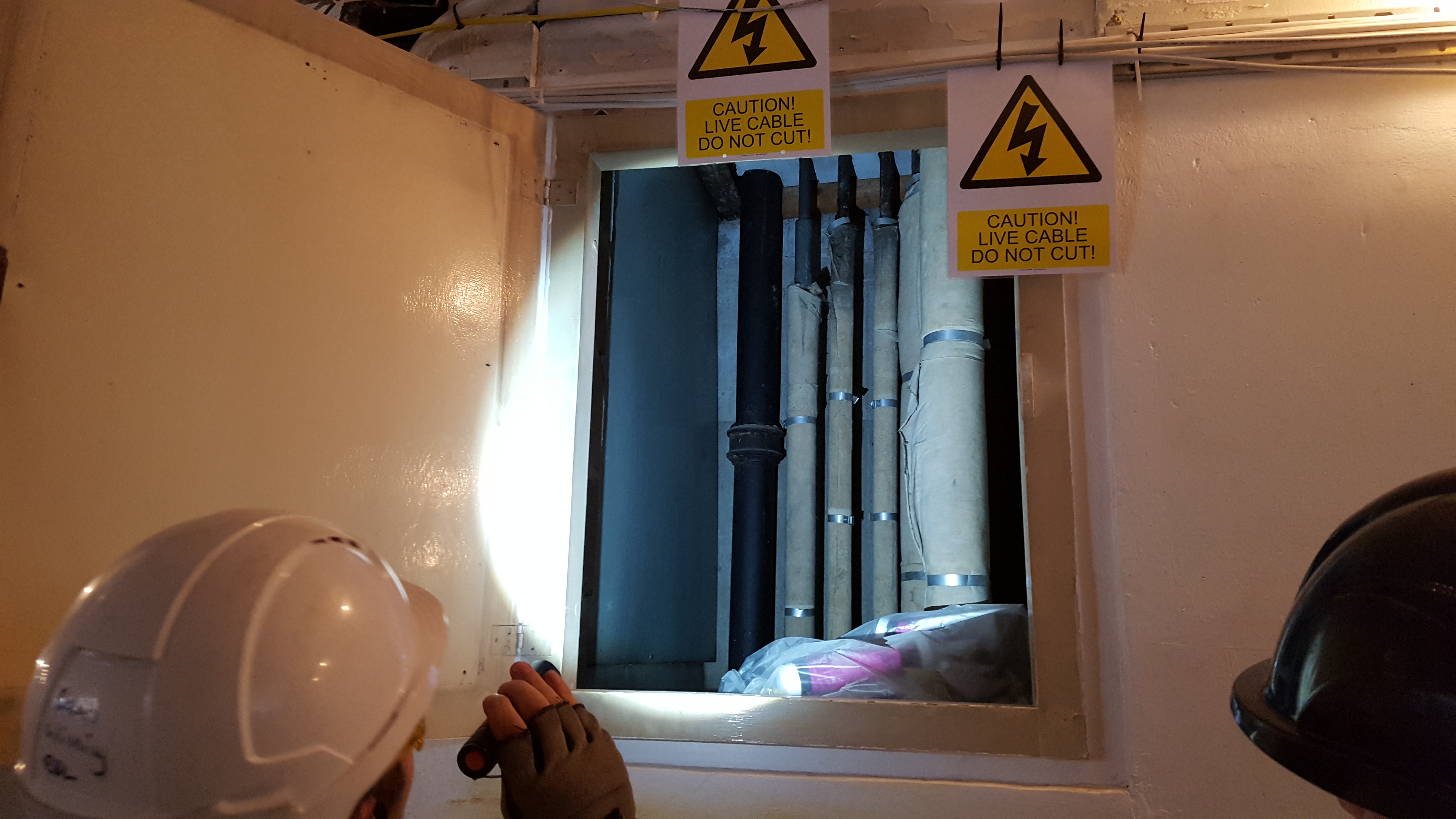
How can you identify RAAC concrete?
RAAC can be difficult to identify visually, as it looks similar to traditional concrete and other building materials. However, there are a few characteristics that can be used to identify RAAC. RAAC is lightweight and porous, making it less dense than traditional concrete. It has a distinct, honeycomb-like structure that can be seen when the material is cut or broken. RAAC has a smooth surface that is free from visible aggregate or coarse materials. How ever so can many asbestos materials especially when painted.
RAAC panels can span between isolated beam supports (steel or concrete) or onto masonry walls (brickwork or blockwork). Typically, panels are hidden behind finishes (suspended ceilings or plasterboard) and therefore may be difficult to identify without minor intrusive works.
Ceiling panels may need to be removed to inspect a roof or access may be required into loft voids. RAAC panels are usually 450mm to 600mm wide and 2.4m to 3m long, although panels were available up to 6m in length.
They typically have a slight chamfer to each edge. The colour varies from white to pale grey. In a roof, the easiest way to identify RAAC panels is to look at the underside although in an occupied building which has been refinished multiple times may be unachievable without intrusive access. Often hidden behind ceiling coverings, it can often be overlooked.
When was RAAC used in schools?
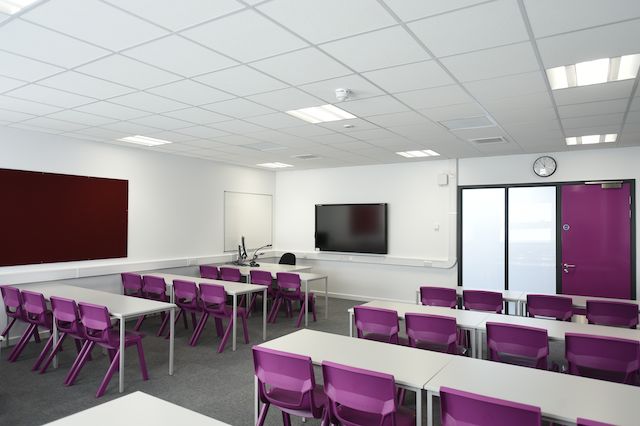
RAAC was used in schools, colleges and other building construction from the 1950suntil the mid-1990s. It may therefore be found in any school and college building (educational and ancillary) that was either built or modified in this time period.
RAAC has been used since the late 1950's and was used extensively up to 1980 with some examples dating to as late as 1998. The material was popular because the planks are considerably lighter with much better thermal insulation properties than conventional concrete planks, making it ideal for flat roofs.
What is the overall condition of school buildings in England?
Schools across the country are in poor condition, with many containing asbestos, or in need of urgent repairs.
In 2019, the DfE referred 676 state-funded schools and academies in England to the HSE overconcerns they were failing to safely manage asbestos in their buildings in line with regulatory requirements, putting thousands of staff and pupils at risk.
About 90% of school buildings in England are thought to contain asbestos, often around pipes and boilers, and in wall and ceiling tiles. The Health and Safety Executive(HSE) advises that it is a risk only if it is disturbed or damaged, which releases fibres into the air.
In 2019, a Guardian investigation found that more than one in six schools in England required urgent repairs. After a series of inspections, surveyors found that almost 4,000 schools across England needed immediate restoration work on roofs, walls or windows, which were deemed in need of immediate replacement or repair.
Many more schools were found not to have the appropriate safety paperwork required by law, including electrical test certificates, fire risk assessments or asbestos management plans.
What should you do next?
In order to be sure that a building isn’t made of RAAC, it's best to first check on the documentation such as building plans and construction records which may indicate if RAAC was used in the construction of a building. If these aren’t present or a professional inspection may be the best next steps.
Why use Summit Environmental for RAAC identification?
About 90% of school buildings in England are thought to contain asbestos, often around pipes and boilers, and in wall and ceiling tiles. The Health and Safety Executive (HSE) advises that it is a risk. Asbestos could easily be disturbed while undertaking investigations for RAAC.
We will follow the government recommendations regarding RAAC identification Reinforced Autoclaved Aerated Concrete (RAAC).Our site experience and understanding of building construction and hazardous materials including concrete testing, hazardous materials, and asbestos.
Our approach is.
Visual confirmation – visual inspection for asbestos materials if no asbestos is visually identified, then continue with visual inspection for RAAC. This is helpful for initial assessments in properties where little or no documentation is available. We can then proceed with either.
· Non-intrusive site sampling – this causes minimal damage and is necessary where destructive sampling poses high risks. This could include taking samples to confirm no asbestos is also identified at the same time.
· Destructive site sampling – this involves removing small pieces of the panel for further investigation. Typically, panels are hidden behind finishes (suspended ceilings, floor finishes, wall linings including plasterboard) and therefore may be difficult to identify without minor or major intrusive works.
Once samples are taken, we can source analytical laboratory testing – which enables conclusive identification of whether a material is RAAC. We do it right because it matters, and we can help.